The Floating fish feed pellet production process plant gives fish food unique taste and color, and adapts to the growing pet food market with the most scientific nutritional ratio and easy digestion.
Because aquatic animals such as fish and shrimp have small intestines and poor digestion and absorption capacity, the processing technology of aquatic feed is far higher than the requirements of livestock and poultry feed processing technology. Therefore, it is particularly important to select aquatic production equipment.
Fish food divided into 2 kinds of fodder, the sinking fish feed and floating fish feed.
This production line can produce aquaculture feed pellets such as squid, grass carp, squid, tilapia, ornamental fish, turtle, and bullfrog.
Fish feed size range: 1mm, 1.5mm, 2.0mm-10mm.
Fish Feed Pellets Processing Technology
Raw Material → Feed Grinding → Feed Mixing → Feed Pelletizing → Pellet Drying → Pellet Cooling → Pellet Crushing → Screening & Grading → Pellet Packing1. Crushing process: It is one of the main processes of the feed mill. The purpose of crushing is to obtain a feed suitable for making high-quality feed and most suitable for animal digestion. The quality of crushing directly affects the comprehensive cost of feed production quality, output and electricity consumption, and also affects the intrinsic quality and feeding effect of feed. The fineness of the aquaculture feed, from the processing cost of feed, the stability of water, the conversion rate of feed and the production performance of aquatic animals, the common freshwater adult fish feed is best able to pass all 40 mesh (420um), young It is best to have 60 mesh (250 um) for all fish; 80 mesh for shrimp and crab feed, and 120 mesh for juvenile shrimp and crab feed.
The pulverization process is closely related to the batching process. According to the combination method, it can be divided into two processes: first batching, first pulverizing and first pulverizing and then batching, or a comprehensive application of the two processes. (
details visit the link:https://www.limapoultrymach.com/waterdrop-feed-hammer-mill.html)
The first batching process after crushing: the raw materials are smashed first, sent to the silo, and then the ingredients are added.
This process: used for the production of adult fish feed for livestock and freshwater fish.
The output of the pulverizer is high, the peak energy consumption is greatly reduced, the pulverization quality is relatively stable, the control is relatively simple, and the pulverizer can be used in parallel to reduce the cost. However, this process requires a larger buffer bin and more silos, the raw material is pulverized too fine, and it is easy to arch after entering the silo, which affects the normal operation of the batching process. In addition, for some high-protein and high-fat raw materials, this process is used to smash the easy-blocking sieve, and the pulverization efficiency is not high.
After the ingredients, the pulverization process: firstly mix the various raw materials according to the ratio, and then pulverize after mixing.
This kind of process: It is more suitable for the production of aquatic feed, especially for special aquatic feeds with high requirements for crushing fineness.
Because it can adapt to changes in material types and physical properties, it can better solve some shortcomings of the first pulverization and batching process. After the various raw materials are mixed, their physical properties are complemented, and it is relatively easy to smash some raw materials which are difficult to pulverize separately with other raw materials. In addition, since the pulverized material directly enters the mixer, the batching bin is saved, and the arching phenomenon of the fine material in the batching bin is solved. The disadvantage of this process is that the pulverizer has a long idle time, low output, and high energy consumption. .
2. Mixing: After the material has been pulverized and compounded, it must be mixed. The mixing uniformity of the mixer is very important in feed processing. It is an important factor affecting the quality of the feed. Therefore, it is very important to choose a suitable mixer. Due to the fine pulverization of aquatic feed, the moisture loss of the material during processing is large (especially after fine pulverization and air transportation). Therefore, adding proper amount of water during the mixing process is beneficial to the processing of the granules, but the added water is required to be atomized. The form is evenly distributed into the material. In addition, because the particle size of the material is too small, static electricity will be generated during the mixing process due to friction, etc., which will affect the uniformity of the mixing, effective grounding treatment of the mixer or anti-static such as adding vegetable oil. Agent can effectively solve this problem. To add vitamins, trace elements, drugs and other small components added to the feed, in order to ensure uniform distribution, it is necessary to pre-mix, dilute stepwise, and then directly pour into the mixer from the opening at the top of the feed mixer for mixing.
4. The design of
granulation process and the selection of related equipment are important factors affecting the quality of aquatic feed. The fish pellet machine used for production is mainly a single-screw extrusion expander, which can be further divided into a dry extrusion extruder and a humidity extrusion extruder. The extrusion equipment currently used is mostly wet and dry. Using different parameters, the extruder can produce buoyant, sinking, slow feed and semi-wet feed, which can adapt to the feeding requirements of various aquatic animals.
Ripening: Ripening is a process in which the feed is subjected to a wet heat treatment to gelatinize the starch, denature the protein, and soften the material. Aquatic feed (especially special aquatic products) is particularly important due to the high water stability and digestibility required. Ripening usually includes two kinds of tempering before granulation and tempering after granulation (post-maturing). They can be used alone or together. Aquatic feeds are usually used together.
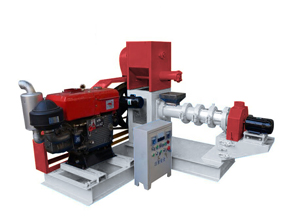
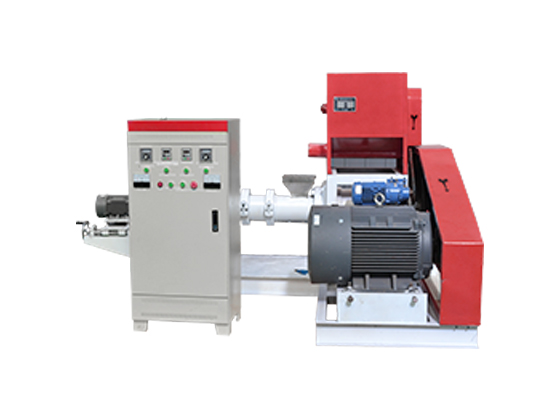
5.Drying:
6. Particle cooling: The hot particles after granulation are post-cured and cooled into a cooler. Since the aquatic pellet feed has high requirements on water resistance, the cooling rate should not be too fast to avoid cracks on the surface of the particles. The application of more cooling equipment is a counter-flow cooler, and the cooling effect is good.
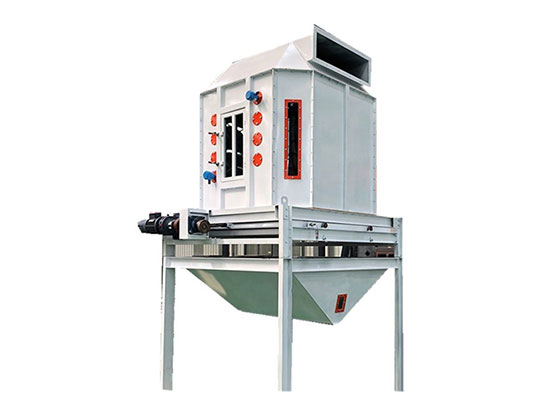
7. Granulator and grading sieve: In principle, the granules should not be used in the production process of hard granule aquatic feed, because the granules will affect the water resistance of the feed, and the granules produced by the extrusion extruder can be obtained by changing the mold. Smaller particles to meet the needs of young aquatic animals, increase productivity and reduce energy consumption.
8. Grading sieve: It is mainly used to screen the feed of the required particle size. The choice of sieve can be determined according to needs.
9. Weighing and packing: